Energy consumption composition of ASU
ASU, especially large scale ASU, has relatively high energy consumption, and the energy consumption composition of ASU mainly includes two aspects:
1、Compressor unit driven by motor (high-voltage power supply, high-power)
Air compressor, booster compressor,(internal compression)
Air compressor, oxygen compressor, nitrogen compressor(external compression)
2、Auxiliary equipment power consumption (low voltage power supply, low power)
Process pumps such as water pumps, cryogenic liquid pumps, electric heaters, oil pumps for various compressors, oil tank heaters, and control systems.
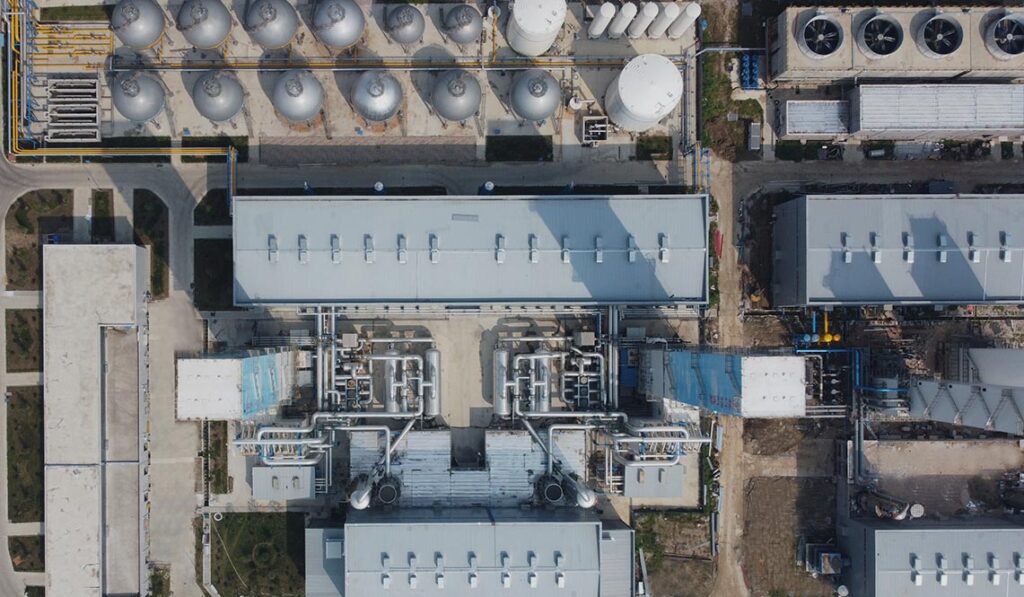
How does ASU save energy and reduce consumption
The energy consumption of the ASU is relatively high. In order to improve the economic efficiency of the ASU operation and also for energy conservation and environmental protection, it is necessary to take some measures to save energy and reduce consumption of the ASU. The measures for energy conservation and consumption reduction of ASU mainly include:
1.Improve the operation efficiency of ASU
- Ensure the use of high quality raw materials such as gas, water and oil.
The ASU also needs to use circulating water during operation, and its quality will affect the entire operating cycle, equipment stability, and reliability. Finally, the mechanical equipment in the ASU also needs to use lubricating oil during use. We should choose high-quality oil when purchasing lubricating oil, and timely lubricate the equipment.
- Improve equipment maintenance monitoring.
The long-term and efficient operation of large scale ASU is inseparable from online monitoring and offline maintenance. In monitoring work, we can promptly identify potential equipment malfunctions and maintain them, thus ensuring the long-term operation of the equipment.
2.Reduce power consumption of ASU
- Reduce the temperature of cooling water.
The compressor unit consumes the most energy in the ASU. In general, we can change the temperature and flow rate of the circulating water to improve the efficiency of the air compressor and control its energy consumption.
- Reduce the pressure of upper column.
In the distillation system of ASU, the initially produced product needs further purification, which requires distillation operations. In distillation operations, the pressure of the upper column is a crucial parameter. If the pressure decreases, the vaporization temperature of liquid oxygen will also decrease. At this time, maintaining a constant pressure in the lower column will cause a decrease in heat exchange between the upper and lower columns, and ultimately lead to pressure decrease in the lower column. After the pressure of the lower column decreases, the pressure of the compressor will also decrease, and the power driving the compressor will also decrease, achieving the goal of reducing energy consumption.
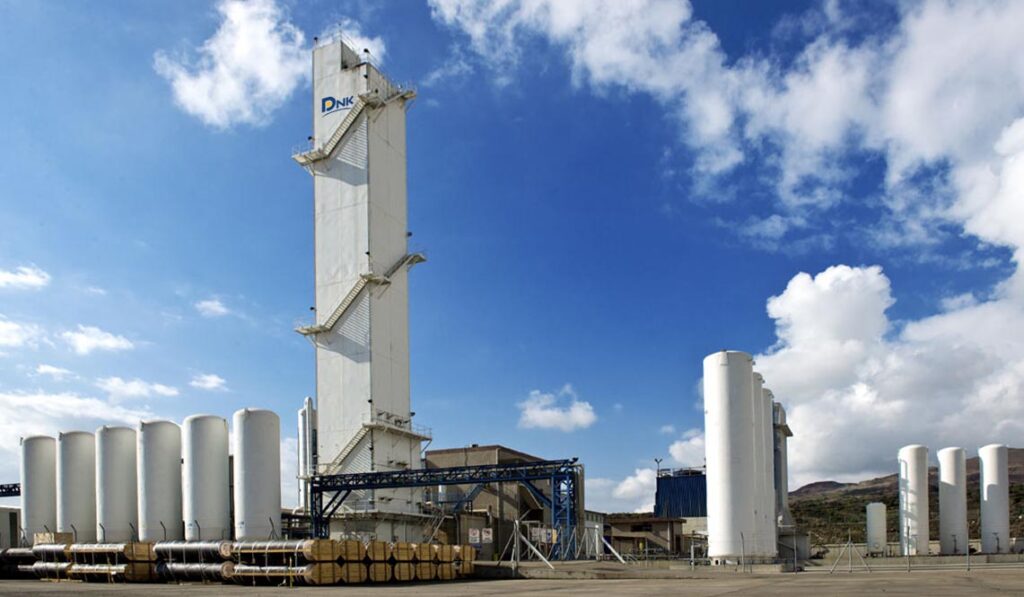
3.Improve product extraction rate and reduce product loss rate
- Control the two balances of ASU
A key parameter for measuring energy conservation and consumption reduction in ASU is the production of other gases such as oxygen and nitrogen per unit time. Its operational efficiency is reflected in the extraction rate of production products. We can use the analysis method of material balance to calculate the material loss of the ASU during operation. At the same time, we can also use the energy balance analysis method to analyze the energy difference between the inlet gas and the output gas, so that we can check the cold loss changes of the ASU during operation and understand the operation of the equipment.
- Control the evaporation loss rate of liquid.
The single gas produced by air separation equipment often needs to undergo liquefaction treatment to facilitate storage and transportation, and the evaporation loss of liquid has become a factor that we cannot ignore. In order to minimize the evaporation loss rate of liquid as much as possible, we need to lower the temperature of these liquid products before entering the storage tank, increase their subcooling, in this way, the evaporation loss rate of liquid products can be effectively controlled.
DINAK AIR SEPARATION
Dinak has 20 years of manufacturing experience and has been focused on developing and optimizing natural gas processing, separation, and liquefaction technologies. Our export volume has also remained at the forefront of the air separation industry for many consecutive years, relying on rich and unique experience to provide high-quality services to global customers in the best way. Tailored solutions for their needs, minimizing energy consumption and improving productivity.