On October 20th, 2022, through the joint efforts of all employees of the participating units,the KDONAr-10000Y/6000Y/300Y air separation unit independently developed and produced by Dinak has successfully started up, successfully produced qualified liquid oxygen, liquid nitrogen, liquid argon and high-purity oxygen products.
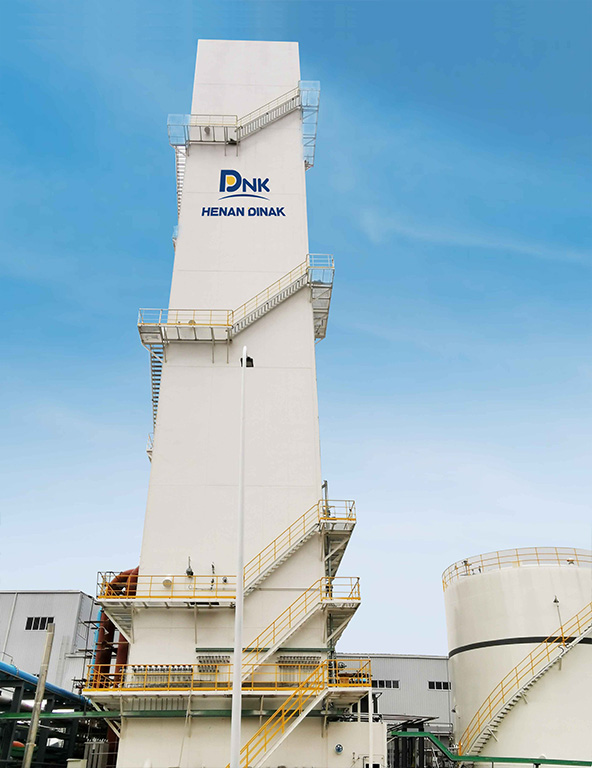
This set of equipment adopts the most advanced air separation technology in the world today: molecular sieve adsorption and purification at room temperature, air circulation, combined refrigeration of high and low temperature turbine expander and low pressure turbine expander, structured packing lower column, upper column and argon column, and can produce high-purity oxygen full liquid air separation process, it is the first domestic high-pressure external gas source liquid air separation unit independently developed by Dinak.
Under project design conditions, the purity of liquid oxygen, liquid nitrogen and liquid argon is much better than the design value,liquid product is rich slightly. The maximum liquid nitrogen working condition is a working condition adjusted to maximize user benefits according to the market price of liquid nitrogen being higher than that of liquid oxygen, during actual operation, the user can freely adjust between the two working conditions according to sales and benefits.
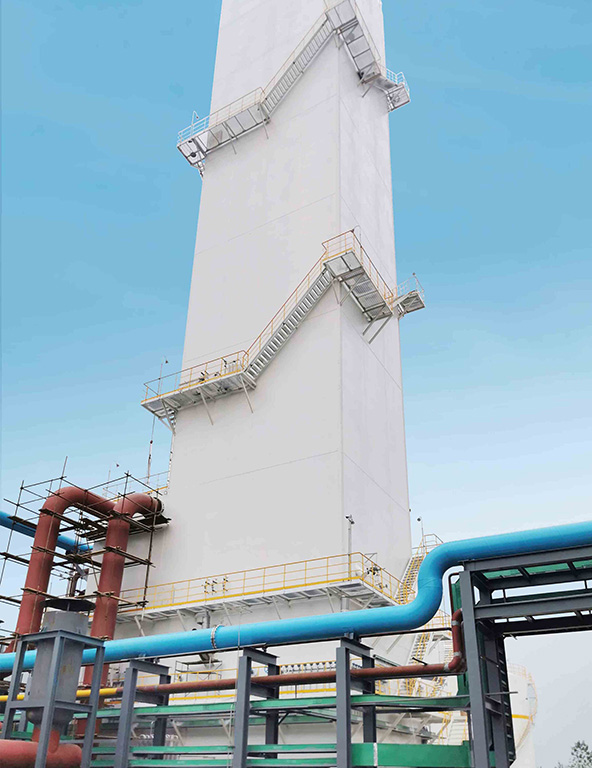
This set of ASU is customized by Dinak according to the client’s specific requirement, self-developed, designed, manufactured amd installed full liquid air separation unit,adpots the full liquid process of room temperature molecular sieve long-term adsorption purification, nitrogen cycle pressurization, high, low temperature and low pressure three booster turbine expanders combined refrigeration, structured packing upper tower, lower tower and full distillation hydrogen-free argon production. It is the first domestic high-pressure external gas source liquid air separation unit, and its main performance indicators have reached the international advanced level.
In view of the high pressure of the external air source, Dinak has fully considered the reliability and safety of the process, involving the selection of process flow, the selection of equipment and valves, the design and installation of pipelines, and the selection and installation of instruments. Ensure that the set of air separation unit can startup safely and smoothly. Mainly include: using high-pressure air heat exchanger instead of air-cooling tower; high-pressure regulating valve using multi-stage pressure-reducing valve; air compressor, air booster compressor, and expander using advanced and reliable products imported from abroad to ensure reliable operation of the ASU.
The one-time test run of this air separation unit was successfully put into production, which is the result of the joint efforts of all employees of Dinak. In the future, Dinak hopes to cooperate with more customers to jointly promote the sustainable development of the air separation field and continue to move towards the direction of green, intelligent, safe and efficient.